Every day we are becoming more vigilant about the way we consume and aim for a better future for our children.
In France, we change tyres every 20 months on average, which represents approximately 150 tyres in a driver’s life!
Wouldn’t it be worth challenging your tyres too?!
Driving BLACK STAR is a confident choice:
LE PNEU RECHAPÉ /RECONDITIONNÉ, C’EST QUOI ?
Give a second life to your tyre !
Retreading allows the reuse of tyres whose rims remain in good working conditions. The tread and sides are replaced according to a specific industrial process and technology to give them a new life without affecting their safety and efficiency. The retreading technique is widely used in demanding sectors such as civil aviation and heavy vehicles. Currently, in the European union, almost one in three truck tyres is a reused tyre.
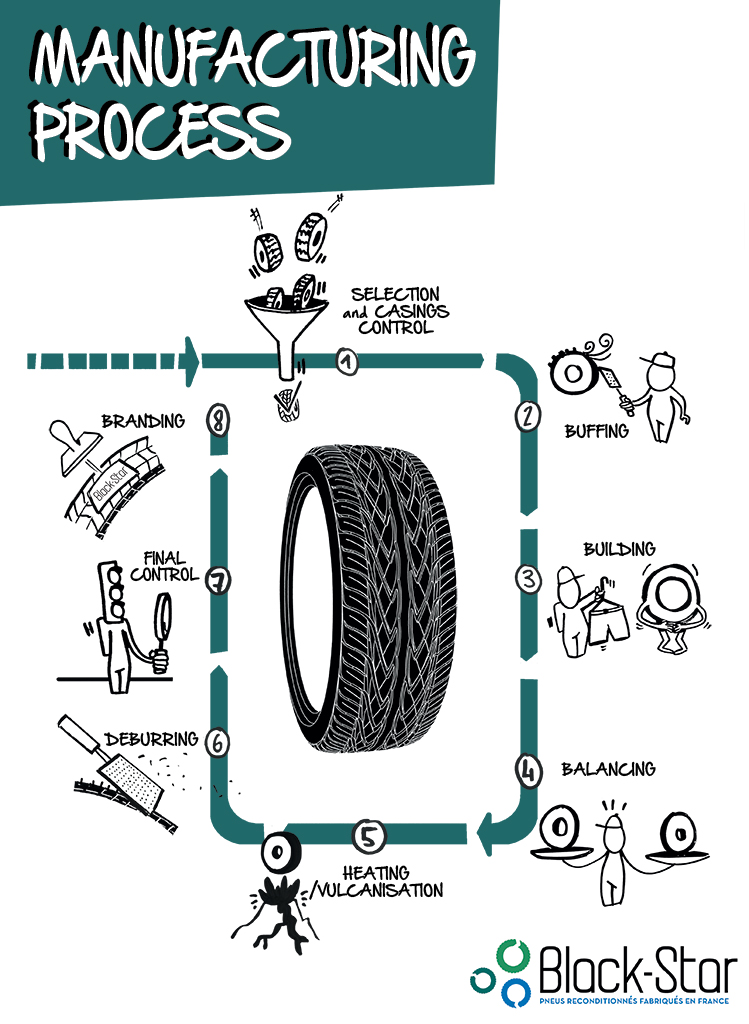
The reused casings (carcass)
At BLACK STAR, it all starts with a meticulous selection of used tyre casings, from the best brands on the market. Next comes a rigorous and manual inspection of the carcass (pressurization, control of the tread, of the sides, calendaring).
A carcass must be in perfect condition to be retreaded. Casings which have been repaired or damaged are eliminated. The control is carried out by our specialists on all the received tyres. Only used tyres whose casing remain in in good conditions will be reused.
Roughening
The roughening phase consists in removing parts of the original rubber from the tread and the sides, in order to obtain a surface capable of receiving new materials. Each grater with digital controls (2 heads, 3 axes) has several thousand programs developed for each dimension, brand and carcass profile. Machine precision is to the millimetre.
Rubber mixing and napping
The grated tyres are then cladded (sidewalls and tread) with a very precise and perfectly regular rubber mix, developed by a manufacturer of new tyres. After the napping, the static unbalance of each tyre is checked and corrected if necessary.
Heating/ Vulcanisation
Installed comfortably in its mould, itself well settled in a press, the tyre goes for a 50 min sauna session ! Just like in the new tyre industry, and to acquire new physical properties, the tyre will be vulcanised (heated) at 155°C and 13 bar pressure for 50 minutes (the vulcanisation time differs depending on the tyre to be retreaded !)
The final control
Each tyred is inspected.
Before getting to the end customer, 100% of BLACK STAR finished products must still be submitted to:
- a final control step (exterior / interior) according to more than 50 criteria (pressurization, control of the tread, sides, calendaring, etc.)
- verification by stereography scanner (same technology for aircraft tyre retreading) in order to detect if the structure has defects visually undetectable (thin separation of the layers, pockets of air occluded under the tread).
And your reconditioned tyre is good to hit the road!
JOIN THE CIRCULAR REVOLUTION!
220 million tyres are fitted and removed every year in Europe. That is about 6 million tons of CO² each year to produce them, the annual equivalent of the CO² emissions of a city of 500,000 inhabitants!
In a world with limited resources, Black Star is betting on the circular economy, reuse, and promoting a multi-life tyre that will offer the lowest carbon footprint on the market.
Fondé en 1979, Black Star est l’unique industriel français spécialisé dans la fabrication de pneumatiques reconditionnés pour les véhicules légers. Il poursuit son objectif de produire des pneus reconditionnés à grande échelle made in France, avec notamment la reprise de l’ancien site industriel Bridgestone à Béthune.
HIT THE ROAD WHILE REDUCING YOUR FOOTPRINT
Let’s face it: we can all be tempted to buy low-cost tyres from distant origins and often designed to be single-used… With BLACK STAR, you offer a new life to the carcass of a tyre and you really reduce your environmental footprint.
Retreading g a tyre also means optimizing its productivity by increasing its mileage output.
Made In France
Black Star embodies “made in France” with its two factories in the territory. It is also a reflection of reindustrialisation, the textbook case of relocation!
Lors de l’annonce de la fermeture de l’usine Bridgestone à Béthune, Black Star et Mobivia (deux acteurs français) ont fait le pari de conserver le métier et l’emploi sur ce site emblématique (47 000 m²).
Black Star appréhende le terme « Ré-emploi » dans sa complétude : réutilisation du site, de l’outil, du savoir-faire métier (obj. 200 emplois), et réutilisation du produit. Les équipes de Black Star n’hésitent pas à mettre l’innovation au service de l’économie circulaire (gisement & distribution), installé dans un écosystème intégré autour de la seconde vie du pneu.